How Often Should You Schedule Packaging Equipment Repair Services?
How Often Should You Schedule Packaging Equipment Repair Services?
Blog Article
Discover Why You Required Dependable Packaging Equipment Repair Service Services for Optimal Production
In the affordable landscape of manufacturing, reliable product packaging devices repair service services play an essential role. Timely treatments can substantially lower equipment downtime and boost manufacturing effectiveness. However, many businesses neglect the value of resolving mechanical failures immediately. This oversight can result in substantial functional obstacles. Recognizing the nuances of repair service services and their ramifications on production can be essential for business going for sustained success. What elements should companies think about to assure they choose the right repair solution?
The Value of Timely Fixes in Production
Although machinery failures are commonly inevitable, the importance of prompt repair work in production can not be overstated. When devices breakdowns, the entire assembly line can be disrupted, leading to costly delays and decreased performance. Makers count on their equipment to operate efficiently; subsequently, prompt fixings are crucial to reduce downtime.Delays in addressing devices concerns can intensify right into bigger issues, influencing product high quality and functional effectiveness. Timely repair work not just recover capability however additionally extend the life expectancy of the machinery, ultimately reducing long-term costs associated with substitutes. Additionally, preserving devices in optimal condition supports work environment security, as defective devices can pose dangers to employees.In the competitive landscape of production, focusing on punctual fixings is essential for maintaining operations and meeting customer demands. Thus, spending in reputable repair service solutions is a strategic move for manufacturers aiming to enhance efficiency and maintain high manufacturing standards.
Typical Issues With Packaging Equipment
Product packaging equipment usually experiences a selection of typical issues that can prevent production effectiveness. One common problem is mechanical failing, which may arise from used components or inadequate upkeep. This can lead to breakdowns that interfere with the packaging process. Another common concern is imbalance, where product packaging machinery stops working to function properly because of inappropriate arrangement, leading to product damages or waste. In enhancement, controls and sensing units can malfunction, bring about incorrect measurements and functional errors.Over time, wear and tear can likewise cause conveyor belts to slip or jam, influencing the flow of products. Furthermore, software glitches in automated systems may result in delays or wrong packaging setups. Normal monitoring and prompt repair work can minimize these issues, making certain smoother procedures. Resolving these typical concerns proactively is vital for keeping optimal efficiency in packaging operations.
Exactly How Devices Downtime Influences Your Company
Exactly how does tools downtime influence a service's total performance and success? Devices downtime can significantly impede a company's procedures, causing lowered production output and postponed distribution times. When equipment stops working, workers may be forced to stand idle, wasting beneficial labor hours and impacting workforce spirits. This disturbance can waterfall via the supply chain, resulting in unmet consumer demands and prospective loss of contracts.Moreover, the monetary implications of tools downtime expand beyond instant losses. Business might experience increased functional prices because of overtime repayments or expedited shipping to meet orders. In very open markets, prolonged downtime can stain a business's online reputation, driving customers towards even more reputable competitors. Eventually, the mix of lost efficiency, increased expenses, and potential reputational damages underscores the vital need for prompt and effective packaging devices fixing services to keep peak procedures and assure sustained success.
Cost-Benefit Evaluation of Specialist Repair Solutions
Reviewing the economic implications of equipment downtime exposes the relevance of professional fixing services. Hold-ups in manufacturing can result in considerable earnings losses, affecting the overall earnings of a service. Purchasing expert repair solutions not only reduces downtime however likewise ensures that equipment operates at peak efficiency.While the first cost of hiring competent technicians might seem high, the long-lasting advantages typically exceed these costs. Trustworthy fixings expand the life-span of equipment, reducing the need for costly substitutes. Additionally, specialist servicing can protect against unexpected break downs that interrupt procedures and incur additional costs (Packaging Equipment Repair Services).Companies that focus on specialist fixing services often experience boosted item high quality and consistency, boosting customer complete satisfaction. Eventually, a well-executed cost-benefit evaluation highlights that the investment in specialist repair work services is not simply an expense, yet a strategic method to safeguarding manufacturing performance and monetary security in the competitive packaging market
Picking the Right Repair Work Provider
When picking a fixing provider, what crucial variables should companies consider to assure perfect results? The service provider's experience and proficiency in maintenance details product packaging devices is fundamental. A firm with a tested track document in the industry can assure that repair work are performed efficiently and effectively. Furthermore, reviewing the company's certifications and training can suggest their commitment to maintaining high standards.Second, responsiveness and accessibility play an essential duty. A dependable repair work solution must use quick action times and versatile check this scheduling to minimize downtime. Third, services need to analyze customer evaluations and endorsements, as these can supply insights into the service provider's integrity and high quality of service.Finally, clear rates and guarantee alternatives are important. A trustworthy provider must provide clear estimates and stand behind their work, assuring that services obtain value for their investment. By thinking about these variables, companies can pick a repair service that fulfills their details needs.
Preventative Maintenance to Prolong Equipment Life Expectancy
Preventative maintenance plays a crucial function in extending the life expectancy of product packaging tools. Carrying out normal evaluation routines, lubrication, calibration, and tactical component substitute can greatly minimize downtime and repair service expenses. By focusing on these practices, organizations can enhance operational effectiveness and warranty reliable efficiency.
Regular Examination Schedules
Normal examination timetables play an important duty in the long life of packaging tools, guaranteeing excellent efficiency and minimizing the chance of unanticipated breakdowns. By sticking to an organized inspection routine, companies can recognize deterioration, attend to possible concerns, and optimize devices capability. These assessments typically involve checking essential components, assessing performance metrics, and reviewing general equipment problem. Normal examinations assist develop a standard for performance, making it less complicated to find variances that may indicate a problem. Packaging Equipment Repair Services. In addition, arranged evaluations can facilitate much better preparation for upkeep and fixings, decreasing downtime and improving productivity. Inevitably, executing normal evaluation timetables adds to an aggressive upkeep strategy that promotes operational performance and prolongs the life-span of product packaging tools
Lubrication and Calibration
Efficient maintenance regimens, such as regular assessments, normally bring about the requirement for lubrication and calibration to assure peak performance of product packaging equipment. Lubrication lessens rubbing, reducing damage on moving parts, which can substantially prolong the life-span of machinery. Regularly applied lube aids maintain operational efficiency, protecting against overheating and prospective break downs. Calibration, on the other hand, guarantees that tools runs within specified parameters, consequently boosting precision and uniformity in manufacturing. Failing to properly oil or calibrate can result in expensive downtimes and fixings. Including these methods right into a preventative upkeep strategy promotes integrity, enhances productivity, and ultimately sustains a stable manufacturing setting. Prioritizing lubrication and calibration is vital for preserving optimal tools capability.
Element Substitute Strategies
An aggressive strategy to component substitute plays a crucial duty in extending the life expectancy of product packaging equipment. Routinely reviewing the problem of crucial components, such as motors, seals, and belts, makes it possible for operators to determine wear and potential failures before they endanger manufacturing. Carrying out a structured timetable for element replacement, based on maker recommendations and use patterns, can greatly reduce downtime and repair service prices. Furthermore, using high-quality replacement components assurances compatibility and performance, better boosting operational efficiency. Training workers to acknowledge early indicators of wear and promoting prompt replacements not just protects against unforeseen malfunctions however also promotes a culture of upkeep awareness. Inevitably, effective element substitute strategies add to important link sustained efficiency and dependability in packaging operations.
Situation Researches: Success Stories From Efficient Services
Looking at real-world examples exposes the considerable effect of reliable packaging tools repairs on operational efficiency. One notable situation included a beverage firm that encountered constant maker malfunctions, leading to considerable manufacturing delays. By partnering with a dependable repair service, they implemented a precautionary upkeep plan that reduced devices downtime by 40%. In one more instance, a treat maker experienced bottlenecks because of malfunctioning sealing machines. After purchasing specialized repair work solutions, they enhanced maker efficiency, resulting in a 30% boost in output.These instances illustrate that timely and reliable repairs not only restore functionality yet also add to enhanced manufacturing prices. By prioritizing effective fixing services, companies can lessen operational disturbances and foster a much more effective environment. Such success tales stress the significance of buying dependable product packaging equipment repair services to protect long-lasting functional performance.
Often Asked Questions
What Credentials Should I Try To Find in Fixing Technicians?
When taking into consideration fixing specialists, one need to focus on qualifications in relevant equipment, experience with certain devices, analytical skills, and a solid record of integrity (Packaging Equipment Repair Services). Good communication and adherence to safety criteria are additionally crucial qualifications to seek
How Can I Identify When My Devices Requirements Repair Works?
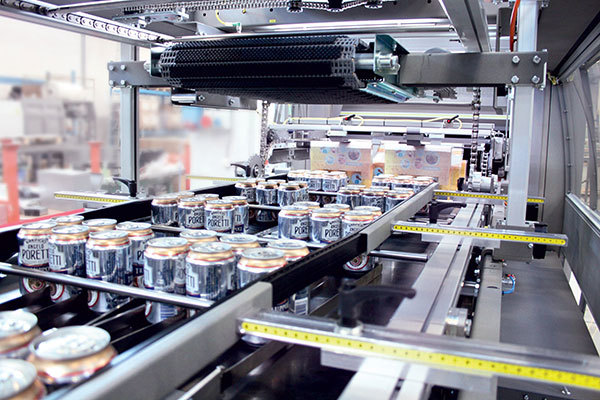
What Kinds Of Packaging Equipment Need Specialized Repair Solutions?

Exist Service Warranties for Repair Work Solutions on Product Packaging Devices?
Warranties for repair solutions on packaging equipment differ by service provider. Usually, respectable companies supply warranties to assure quality and integrity, covering parts and labor for a given duration, consequently boosting customer self-confidence in their solutions.
Exactly how Do I Set Up Emergency Repair Service Providers?
To set up emergency situation repair service services, one usually contacts the company directly by means of phone or their website. Motivate interaction assurances a speedy action, permitting timely resolution of equipment problems and lessening manufacturing interruptions. In the affordable landscape of production, trustworthy packaging devices repair solutions play a crucial function. In addition, maintaining equipment in optimal problem supports workplace security, as malfunctioning equipment can posture hazards to employees.In the competitive landscape of production, focusing on punctual repair services is important for sustaining operations and conference customer needs. After spending in specialized repair service services, they boosted equipment efficiency, resulting in a 30% boost in output.These instances show that prompt and efficient repair work not just bring back functionality however likewise add to better production prices. Specific types of product packaging tools, such as vacuum cleaner visit their website sealers, labeling machines, and automated conveyors, commonly need specialized fixing services. Service warranties for repair solutions on packaging equipment vary by service provider.
Report this page